一、传统工业界面为何难以满足智能化需求?
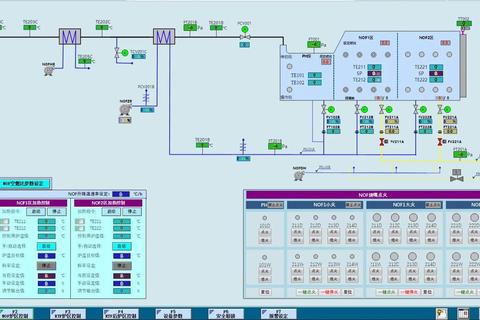
在工业4.0时代,工厂设备每天产生海量数据,但许多企业仍在使用“按钮+指示灯”的传统人机界面。数据显示,超过60%的操作员因界面交互复杂导致误操作,而设备停机维修时间中有35%源于人机交互效率低下。这种矛盾引发行业争议:工业交互是否注定要在效率与复杂度之间二选一?
台达触摸屏编程软件通过“高效赋能智能操控 台达触摸屏编程软件革新工业交互体验”的核心理念,给出了破局答案。以汽车零部件厂商为例,其生产线曾因设备参数调整耗时过长,导致日产能损失12%。引入台达DOPSoft软件后,通过定制化界面和实时数据看板,设备调试时间缩短40%,验证了智能交互对生产力的直接赋能。
二、如何用编程软件实现“零代码”高效操控?
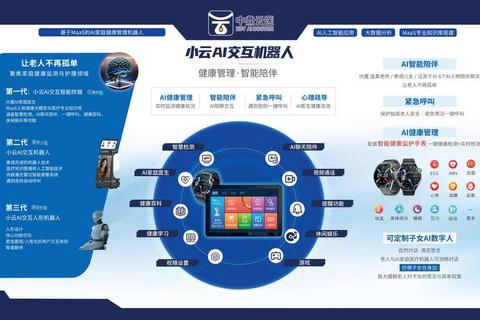
传统工业界面开发需工程师编写数百行代码,而台达DOPSoft的图形化设计彻底改变了这一模式。其元件库内置200+预制控件,如动态曲线图、多语言切换模块等,用户通过拖拽即可完成80%的界面搭建。某食品包装机械企业利用该功能,仅用3天便开发出支持中英双语的生产监控系统,较传统方式提速5倍。
更突破性的是Lua脚本与宏功能的融合。在半导体晶圆厂案例中,工程师通过编写宏指令实现“一键切换工艺配方”,将原本需要15步的操作简化为单次触控,并使设备兼容性提升至8种不同规格晶圆生产。这种“高效赋能智能操控 台达触摸屏编程软件革新工业交互体验”的技术路径,让非程序员也能参与复杂逻辑设计。
三、动态交互如何破解设备孤岛难题?
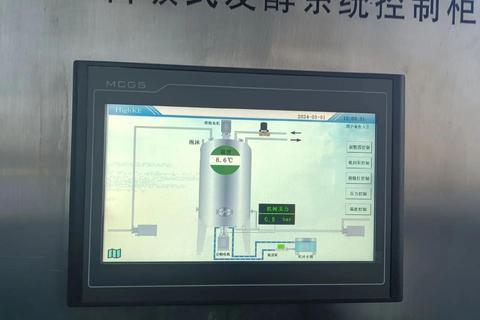
工业现场常面临PLC、变频器、机器人等多品牌设备协同难题。台达软件通过MODBUS、CANopen等23种通讯协议库,构建了真正的“全厂互联”界面。一家纺织企业曾因西门子PLC与三菱伺服系统无法协同导致次品率攀升,采用台达AE系列触摸屏后,通过协议转换功能实现数据互通,良品率回升至99.2%。
在扩展性方面,软件支持IoT云平台对接。某智慧水务项目通过DOPSoft V4版本,将分布在20公里管网的50台泵站数据实时映射至中央大屏,并集成AI算法实现故障预测,使应急响应时间从2小时压缩至15分钟。这正是“高效赋能智能操控 台达触摸屏编程软件革新工业交互体验”的具象化体现。
四、未来工厂需要怎样的交互设计思维?
对于企业而言,选择台达方案需把握三个关键:
1. 场景化选型:基本型B系列适合单机设备,而支持以太网的AE系列更适合联网工厂;
2. 模块化开发:利用行列式清单功能,将工艺流程参数封装为可复用模块,如某注塑机厂商借此实现30种产品参数的快速切换;
3. 数据驱动迭代:通过软件内置的OEE(设备综合效率)分析工具,某汽车焊装线每月优化5%的交互流程,累计提升产能18%。
“高效赋能智能操控 台达触摸屏编程软件革新工业交互体验”不仅是技术升级,更代表着工业人机交互从“功能实现”到“价值创造”的范式转移。当操作员能通过直观的触控手势指挥整条产线,当设备数据转化为可执行的商业洞察,工业4.0才真正走向落地生根。
相关文章:
文章已关闭评论!