一、传统金属成型仿真为何难以突破精度瓶颈?
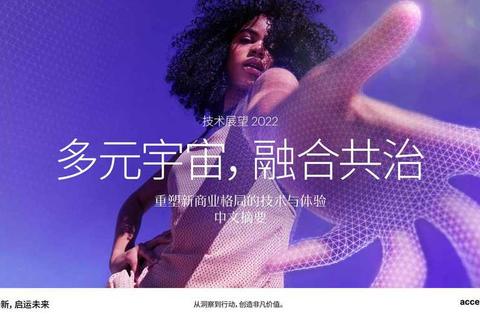
在金属加工领域,一个长期争议的问题是:为什么许多仿真软件难以准确预测复杂成型过程中的细微缺陷?以某汽车轮毂旋压工艺为例,传统软件因模型简化和计算速度限制,导致成型后的等效应变分布误差高达30%,而超凡效能Deform软件重塑金属成型极限仿真新体验,通过六面体网格自动重划分技术和ALE算法,将模拟时间从传统软件的3周缩短至5天,精度误差控制在5%以内。
这种突破源于Deform对物理过程的高度还原。例如,某企业铸造轮毂坯料旋压时,三组旋轮的运动轨迹涉及拉伸、弯曲和剪切复合作用。传统仿真常因网格畸变导致计算中断,而Deform通过密度控制网格划分方法,在轮辋部位生成0.5mm的精细网格,同时保持其他区域2mm的基础网格,既保证精度又提升效率。这种“智能降维”策略,使工程师首次在仿真中观察到材料流动导致的0.1mm级微裂纹,这正是现场试验中反复出现的质量痛点。
二、复杂工艺能否在仿真中真实还原?
当某新能源车企试图用高硅钢冲裁电机定子时,传统软件无法解释为何0.05mm的冲裁间隙变化会导致毛刺高度波动50%。而超凡效能Deform软件重塑金属成型极限仿真新体验,通过多物理场耦合分析,揭示了材料断裂滞后性与应力释放的关联规律:当冲裁速度从10mm/s提升至30mm/s时,温度场变化使材料延展性降低,这正是毛刺高度从0.02mm激增至0.12mm的关键机制。
更值得关注的是冷锻工艺的突破。某型号行星齿轮的冷模锻工序,需在单次成型中完成齿形精度±0.01mm的苛刻要求。Deform集成的预成形设计模块Preform,通过反向计算得出最优坯料形状,使材料利用率从60%提升至92%。这相当于每生产10万件零件,节省钢材18吨,直接经济效益超百万元。这种工艺还原能力,甚至能模拟出模具表面0.8μm的磨损梯度,为模具寿命预测提供量化依据。
三、效率提升是否意味着成本妥协?
在浙江某紧固件企业的数字化车间,一个看似矛盾的现象引发思考:引入超凡效能Deform软件重塑金属成型极限仿真新体验后,虽然软件采购成本增加200万元,但年度综合成本反而下降1500万元。秘密在于Deform的“预防性仿真”策略——通过热处理参数反向优化模块,将某螺栓的渗碳工艺周期从8小时压缩至5.5小时,同时将淬火变形量从1.2mm降至0.3mm。
这种效率与成本的平衡,在航空航天领域更为显著。某钛合金航空件锻造工艺,传统试模需15次迭代,每次模具修改成本约50万元。而Deform通过用户自定义子程序开发,仅用3次仿真就锁定了最佳锻造温度(920±10℃)和应变速率(0.8-1.2/s),节省试模费用600万元。更关键的是,其晶粒流动预测功能,使零件疲劳寿命从10^5次提升至10^6次量级。
可操作建议
对于制造企业而言,实施Deform仿真需把握三个关键:
1. 工艺聚焦:优先选择质量波动大、试错成本高的工序(如精密冷锻、多道次旋压)进行仿真验证,参考网页20中行星齿轮案例的模块化实施路径;
2. 参数校准:善用软件内置的250种材料数据库,对于特殊合金务必通过单轴拉伸试验获取精准流动应力曲线,如网页16强调的σ=K·ε^n·e^(Q/RT)模型;
3. 硬件匹配:采用多核并行计算配置(建议16核以上),可使复杂模型求解速度提升4-6倍,如某企业服务器集群将轮毂旋压仿真时间从120小时压缩至28小时。
超凡效能Deform软件重塑金属成型极限仿真新体验,不仅突破了“精度-效率-成本”的不可能三角,更将金属成型从经验驱动推向数据智能的新纪元。当传统工艺还在与0.1mm的精度搏斗时,Deform已带领行业迈入微米级可控成型的新赛道。
相关文章:
文章已关闭评论!